Blog
Automotive Construction: Full Throttle or Pump The Brakes?
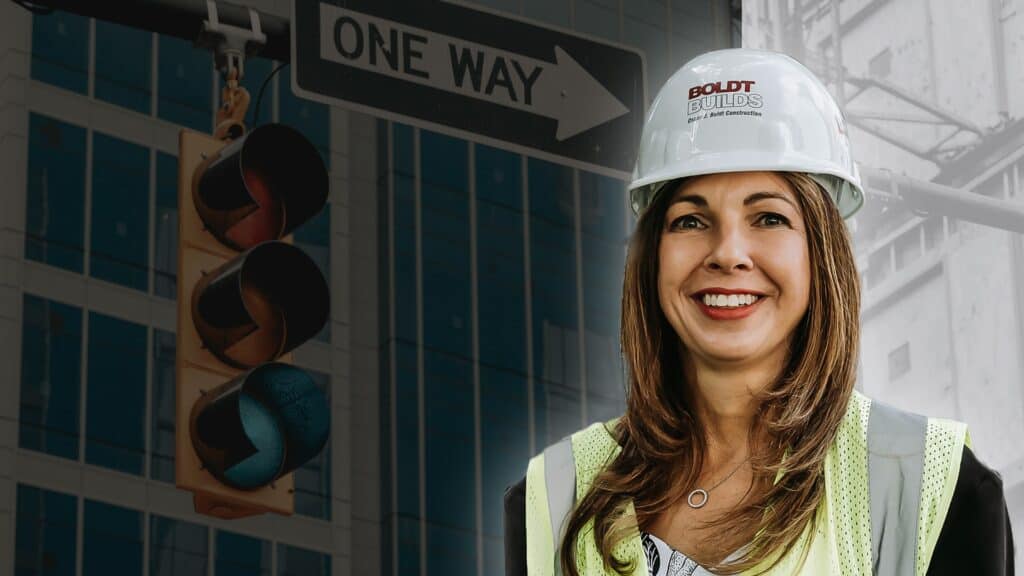
From Electric Vehicles to labor shortages, Boldt’s Linda Rosati takes us behind the wheel of what’s driving the trends in automotive plant construction
The automotive industry is evolving at an accelerated pace. Global supply chain disruptions threaten to continue to rock the industry as automakers seek to meet demand for everything from microchips to raw materials. Traditional auto makers and venture capital-backed startups battle for market share of the burgeoning Electric Vehicle (EV) space, with significant capital being spent on increasing production capabilities in the U.S. In the background, regulations, and infrastructure struggle to keep up with innovations in autonomous vehicles and EV power demand.
But where is it all headed? To find out, we sat down with Linda Rosati, Boldt’s Director of Business Development. Linda has spent most of her 25+ year career in the automotive and construction industries and shared her insights on overall market trends, newcomers to the EV space, autonomous vehicles, supply chains and raw materials, and overcoming construction challenges.
Can you tell us about your role at Boldt and how you got started in the industry?
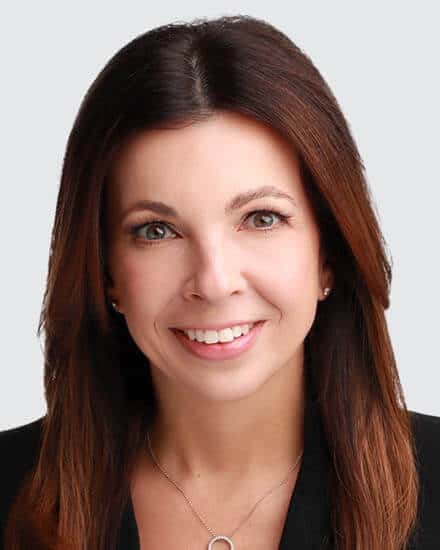
Business Development Director
I serve as Business Development Director in Boldt’s Detroit office, but I help build and service our client and partner relationships nationwide, primarily in the automotive and industrial/manufacturing industries.
My dad can take credit for getting me started in the auto world. He worked in the machine tool industry and would do contract design work at night at home. He taught me the basics of drafting and how to make calculations and formulas to use with my designs. Eventually, I was able to use what he taught me to get a job as a designer and, aside from a brief hiatus in real estate sales, I spent most of the next couple of decades in the automotive and manufacturing industries.
At Boldt, I use my industry knowledge and understanding of client needs to help tailor our construction and contracting services to better meet them. It’s interesting being on the other side of the table but also very rewarding getting to work with our large, established automotive clients and emerging EV companies alike on some pretty exciting projects.
What’s the current state of the automotive construction industry?
There’s a lot of positive movement right now. Auto makers are making large investments in new and existing plants in the U.S. We’ve seen focus in the media on the newcomers in the EV auto space, but there’s been heavy investment in EV from the traditional “Big Three” as well. GM, for example, announced plans late last year to invest more than $3B in EV projects right here in Michigan. The amount being built or in various stages of planning and development is a big shift from recent decades.
“…the early predictions on how quickly we’ll get [to autonomous vehicles] is shifting outward, largely due to infrastructure needs, insurance requirements and policies and regulations surrounding safety.“
The other big push is to get to fully autonomous vehicles. While there’s a lot of excitement around it, the early predictions on how quickly we’ll get there is shifting outward, largely due to infrastructure needs, insurance requirements and policies and regulations surrounding safety. I can’t personally say when we’ll get there, but based on observations and the conversations we’re having, I would say we’re still 15-20 years out yet from seeing Level-5 and 6 automation – what most of us picture as self-driving – on the road.
You mentioned large-scale investment in facilities. How long do you see that trend continuing?
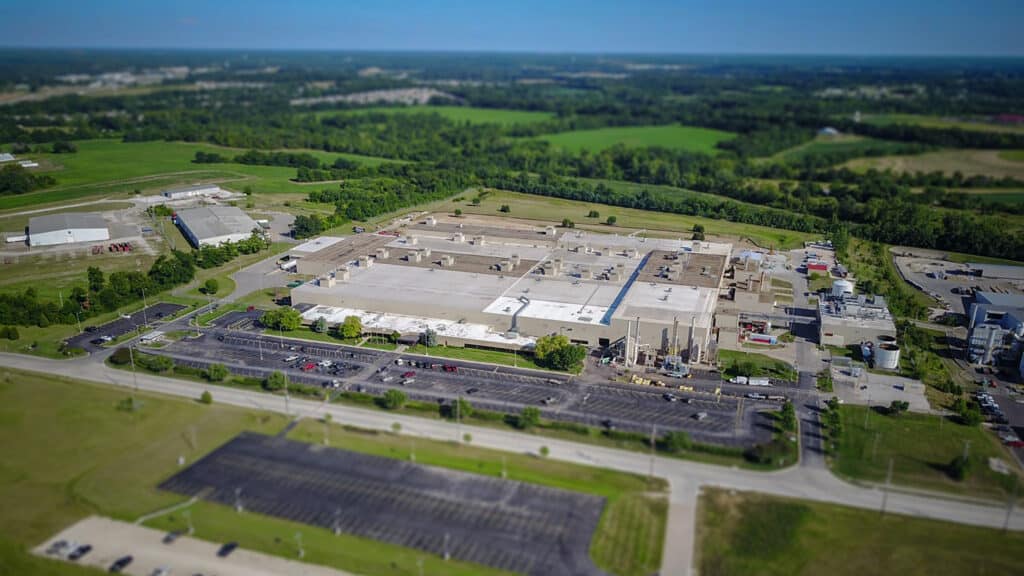
The EV market, which is what’s driving a lot of investment, is a bit of an unknown currently. There are new companies emerging that have serious investment capital, some backed by government and business investment, but it remains to be seen how they’ll handle scaling to meet production while continuing to secure new capital. Ultimately, consumer demand is going to determine how sustainable this is in the long-term. We still have a way to go before that outpaces demand from government entities, or new fleet vehicles for private enterprises like Amazon and others.
I believe we’ll see a leveling out of these large projects in the not terribly distant future and the playing field will narrow as EV market leaders emerge. After that, we’ll likely see more larger-scale projects up and down the supply chain in parts manufacturing and supporting infrastructure, while the automakers shift back to facilities maintenance, retooling and upgrades.
Can you elaborate what this might mean for those secondary and tertiary parts manufacturers?
It will be challenging for newer EV start-ups to achieve 100% vehicle build right away, so they may choose to go out to other suppliers to make their frames, or paint their bodies, etc. With the industry focused on achieving lean manufacturing, just-in-time delivery means these suppliers will need to open nearby operations and invest in warehousing and distribution capacity to support that. For something like battery storage, which has stringent fire safety guidelines, it’s going to take experienced contractors to deliver them.
What challenges are those companies facing with construction?
In a word: shortages. Most people are familiar with some of the supply chain issues facing automakers related to manufacturing — chip shortages especially. What is less familiar to many are the pressures on the supply chain related to the construction of these facilities, from raw materials to building products. As companies take on these large projects, their primary focus is speed to market so they can start producing vehicles sooner. Because of material supply chain issues and market volatility, projects costs can quickly escalate beyond initial estimates and face delays.
The other big challenge is with a shortage of skilled construction labor. Many of these projects are occurring in places already facing a shortage of skilled tradespeople, so labor costs are at a premium while subcontractor choice is thin. As a result, clients get fewer, less competitive bids, potentially leading to lesser quality of work and higher prices.
What steps is Boldt taking to help address those for their auto clients?
Number one is early contractor engagement. Early, upfront collaboration between the client, the engineer or architect and the contractor means identifying and developing solutions for challenges before they become costly delays. Companies that use the traditional hard-bid delivery miss out on opportunities for cost and schedule savings because once the drawings are finalized and the schedule set, they’re too late to avoid.
“Early, upfront collaboration between the client, the engineer or architect and the contractor means identifying and developing solutions for challenges before they become costly delays.“
Our experience up and down the supply chain, from mining and energy production to maintenance facilities, gives us great insight into potential challenges and opportunities for synergy but it’s largely wasted unless we’re brought to the table early.
What about those skilled labor shortages?
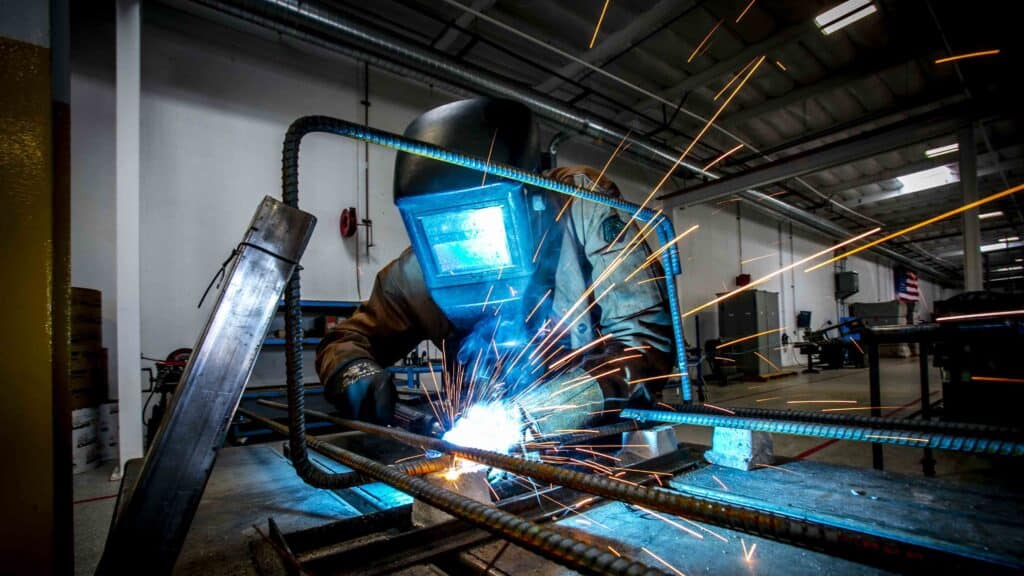
We self-perform many key trades needed for our clients’ construction projects, especially with equipment rigging and installation. That means less reliance on subcontractors and local labor. We’ve also invested heavily in our prefabrication capabilities, letting us move more construction off-site into controlled environments. This gives us a wider degree of latitude as far as staffing is concerned and can cut construction schedules down substantially. It also has the added benefits of defect-free production and safer, less congested jobsites.
The auto industry shed nearly 100,000 jobs during the pandemic, which includes facilities staff. Our clients appreciate the access to our experienced maintenance teams. They’re highly trained, experienced, and available at the drop of a hat, 24/7. As the building boom matures, maintaining and upgrading existing facilities is going to be crucial.
Do you have any closing thoughts you’d like to share?
This is just an exciting time in the auto world right now, probably more so than any time in the last thirty years. I’m grateful that Boldt is right in the middle of a lot of it and that I get to see it firsthand.
About The Boldt Company
The Boldt Company (Boldt) is a leading professional construction services firm with customers across the United States and is a subsidiary of The Boldt Group. Founded in 1889, Boldt is a fourth-generation family and employee-owned firm headquartered in Appleton, Wisconsin. Boldt is recognized as a pioneer in Lean construction and in the industrialized construction space. Boldt operates 18 offices across the U.S. that serve customers in healthcare, power, industrial, education, automotive and commercial markets.